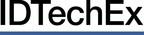
IDTechEx Discusses Ag Sintering and Cu Sintering
BOSTON, June 5, 2024 /PRNewswire/ — Thermal management for EV power electronics has long posed significant challenges. The ongoing shift from Si IGBT and SiC MOSFET to potentially GaN HEMT in the future results in higher junction temperatures and increased demand for die-attach materials in EV power modules. In traditional Si IGBT power modules, die-attach materials like Pb95Sn5 and Pb92.5Sn5Ag2.5 struggle to meet reliability requirements for packaging power devices in high-temperature applications due to creep-fatigue concerns. Additionally, substrate-attach materials such as Sn96.5Ag3Cu0.5, with lower melting temperatures than solder used for die attachment, further constrain the reliability of SiC power modules for high-temperature applications. These challenges drive the market toward silver sinter materials, with the potential to extend to copper sinter materials, offering cost reductions.
Despite cost advantages, the IDTechEx report “Thermal Management for EV Power Electronics 2024-2034: Forecasts, Technologies, Markets, and Trends” identifies barriers hindering the widespread commercialization of copper sintering, such as challenging manufacturing environments due to copper oxidation and comparable or even higher costs than silver sintering as of early 2024 due to smaller commercialization scales.
Conventional die-attach and substrate-attach materials typically consist of solder alloys, featuring bondline thicknesses ranging from 50 to 100µm for die attachment and 100 to 150µm for substrate attachment. Despite their satisfactory performance, IDTechEx observes a growing preference for Ag sintering, driven by major automotive OEMs like Tesla, BYD, and Hyundai. Compared to traditional solder alloys, Ag sintering offers higher thermal conductivity (between 200 and 300W/mK), potentially reducing thermal resistance from junction to case by over 40%, along with significantly higher melting points and decreased electrical resistivity.
With the adoption of SiC MOSFETs, IDTechEx forecasts that Ag sintering will capture nearly or over 50% market share in regions like China in the near future, presenting significant market opportunities for thermal material suppliers.
Much of the available sintered Ag on the market requires pressure during sintering to enhance bond characteristics and reduce porosity, significantly reducing sintering time. However, this approach has drawbacks, including decreased yield and efficiency for bonding multiple chips, especially with complex architecture. Further, it also requires additional steps and machines, leading to higher costs. Therefore, manufacturers tend to avoid this and wait for solutions that are easy to implement in their already existing infrastructure: pressure-less sintering. Pressure-less sintering offers lower cost barriers and benefits in sinter-bonding multiple chips but is reliable only for surfaces with areas between 4 and 25mm2. More details about the pressure-less sintering process are included in IDTechEx’s report, ‘Thermal Management for EV Power Electronics 2024-2034: Forecasts, Technologies, Markets, and Trends’.
The cost of Ag sintering can vary significantly based on factors like customer relationships, order volumes, and suppliers. Ag sintered paste costs can easily be five to ten times higher than solder alloys. For instance, IDTechEx learned of an Ag sintered paste developed by a Japanese company costing around US$2-3/g, though this price has the potential to decrease significantly with increased volume and other material properties. Another supplier suggests that its sintered silver paste costs around US$1,400/kg. Overall, driven by leading automotive players, there is a discernible trend toward replacing solder alloys with Ag sintering pastes, creating market opportunities for material suppliers.
Cu sintering is proposed as an alternative approach to address the cost factor. Compared to Ag sintering, Cu sintering aims to offer similar performance at a lower cost. A supplier informed IDTechEx that Cu sintering technology can cost as little as half as much as Ag sintering technology. However, oxidation remains a significant challenge for Cu sintering. Therefore, a combination of a controlled atmosphere and reducing solvent/binders is the focus on the production of reliable materials. Cu sintering pastes have pressure and pessure-less variants under N2 or H2. However, this presents challenges during processing, leading to concerns around reliability.
IDTechEx is not aware of any automaker using Cu sintered materials as of early 2024, but given the historic timeline for Ag sintering adoption, IDTechEx forecasts that the large-scale commercialization will happen within five years and potentially as soon as late 2024 or early 2025.
IDTechEx’s ‘Thermal Management for EV Power Electronics 2024-2034’ provides a comprehensive overview of Ag and Cu sintering technologies market opportunities, competitive landscapes, supply chains, and key players in the substrate-attach and die-attach sectors. To find out more about this report, including downloadable sample pages, please see www.IDTechEx.com/TMPE.
IDTechEx has also published a report on thermal interface materials, which includes details on die-attach and TIM2s for other emerging applications, including advanced driver-assisted systems (ADAS), 5G, data center semiconductors, EV batteries, and consumer electronics. To find out more about this report, including downloadable sample pages, please see www.IDTechEx.com/TIM.
For the full portfolio of thermal management market research from IDTechEx, please visit www.IDTechEx.com/Research/Thermal.
About IDTechEx:
IDTechEx provides trusted independent research on emerging technologies and their markets. Since 1999, we have been helping our clients to understand new technologies, their supply chains, market requirements, opportunities and forecasts. For more information, contact [email protected] or visit www.IDTechEx.com.
Media Contact:
Lucy Rogers
Sales and Marketing Administrator
[email protected]
+44(0)1223 812300
Social Media Links:
Twitter: www.twitter.com/IDTechEx
LinkedIn: www.linkedin.com/company/IDTechEx
Logo: https://mma.prnewswire.com/media/478371/IDTechEx_Logo.jpg
View original content:https://www.prnewswire.co.uk/news-releases/idtechex-discusses-ag-sintering-and-cu-sintering-302164662.html